Pictured above: Joe Rangel (in tan jacket) and Leo Boedigheimer work in the Fort Vancouver High School welding shop, where Joe has flourished. Photos by Cheryl Boatman.
Finding a home
Jose Rangel—Joe as he’s known at school—loves working in the welding shop. After watching his father weld and wanting to learn, Joe joined Fort Vancouver High School’s welding program in fall 2017. He underwent safety training and now can solder, MIG weld, torch weld, use a grinder and do iron work.
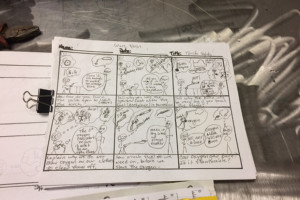
Boedigheimer draws sketches to explain new information to Rangel.
One thing this junior won’t do: let his vision and communication challenges or his significant hearing loss hold him back. With the help of his interpreter, Leo Boedigheimer, Joe has developed fundamental skills that can be used to prepare parts for robotic welding, for example.
Welding also was new for Boedigheimer last fall. The pair has advanced their skills together. To help Joe process new information, Boedigheimer sought special training from welding teacher David Richards. Boedigheimer uses those tutorials to inform the sketches that he creates to assist Joe in tracking processes and daily schedules.
Joe has flourished in the welding program, according to Richards, and now Joe says he wants a welding job when he finishes school.
“Out here [in the program], he’s found a home,” said Richards.
Measuring success
Richards is a firm believer that success in the welding industry is measured in jobs. Not just any jobs, but ones in welding and related fields that require highly skilled workers and pay living wages. He marks that success literally. The wall outside his office bears the signatures of former students working in welding and related positions with annual salaries in excess of $50,000. To date, there are more than 15 names on the wall. Richards can name at least another 30 who haven’t yet signed. Many secured these salaries within just a few years of finishing high school.
Preparing students for workplace standards and safety requirements is as important to Richards as teaching hard skills. Graduates of the program leave Fort with certification from the Occupational Safety & Health Administration. Many also leave with employment offers.
“I try to treat the kids not like they’re high school students. I try to teach them like employees. When they hit the real world, they’re not going to have a shock of transition,” Richards said.
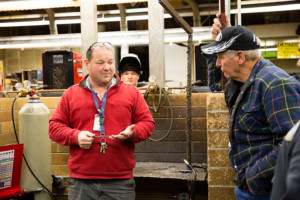
David Richards, in red, explains wire feed welding to VPS employees Craig Witt and Julio Valencia (not pictured) while Matt Johnson looks on.
When he started 15 years ago as a part-time instructor at Fort, Richards thought big: Why not build a hovercraft? How about utility trailers and custom recumbent bicycles?
As the projects grew in scope, so did enrollment in the program and partnerships with other Fort programs and with businesses including Papa Johns and Frito Lay. More recently, a local McDonalds franchise awarded the program $2,000 to provide cutting-edge equipment needed for welding restaurant-grade stainless and aluminum metals.
Seeing the program gain recognition in the community is rewarding, but as Richards prepares for a new role outside of the district, he says what he’ll miss the most are the students like Joe and the hundreds who have passed through the shop where they forged new skills and friendships.
“Watching the growth is fun. To have kids come in not knowing much about welding and come out of here capable young men and women is the goal,” he said.